14 Surface Treatments That Matter: A Closer Look at Fastener Finishing
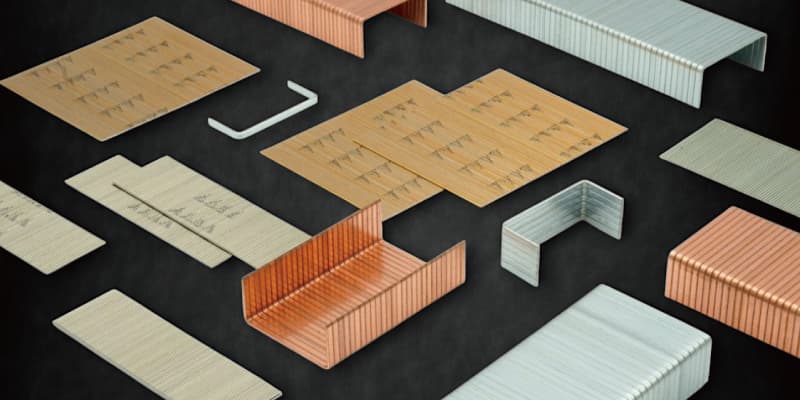
In the world of fasteners, performance starts at the surface—with the right finishing. Whether applied for function or aesthetics, every coating layer contributes to the fastener coating system that determines corrosion resistance, wear protection, and integration with surrounding materials. Today’s finishing technologies are essential for fasteners used in demanding environments, from industrial manufacturing to outdoor framing, where a reliable coating is not optional—it’s critical.
This article explores the most widely used finishing and coating types in the industry. We compare their chemical properties, protective capabilities, and ideal applications to help you select the most suitable fastener coating—whether for nails, staples, screws, bolts, or nuts.
What Is Finishing?
Fastener Coating and finishing refer to the surface treatments applied during manufacturing to enhance a product’s durability, corrosion resistance, and visual appeal. These coating systems are crucial for fasteners operating in environments with high humidity, chemical exposure, or constant mechanical wear. The right finishing not only prevents rust and reduces staining on exposed surfaces but also meets stringent technical demands across industries—from woodworking and packaging to exterior construction.
Whether used on nails, staples, screws, bolts, or nuts, a well-chosen fastener coating can significantly reduce installation issues, minimize callbacks, and extend the service life of every project. Ultimately, effective coating solutions improve both performance and customer satisfaction.
Types of Fastener Finishes
A variety of fastener coatings are used in today's Nails Finishing, Staples Finishing, and Screw Finishing processes, each offering distinct advantages based on the material, environment, and intended application.
Bright Finish (BR)
An uncoated finishing option for carbon steel fasteners, Bright Finishing leaves a clean, metallic surface ideal for indoor use in dry, non-corrosive environments. This coating is cost-effective but provides no rust protection, making it suitable only for non-exposed applications.
Used in: Coil nails used in interior woodworking where exposure to moisture is not a concern.
Galvanized Finish (Galv., also known as Electrogalvanized Finish)
Electrogalvanized coating applies a thin layer of zinc through electroplating, offering moderate corrosion resistance and a uniform, shiny appearance. It is a versatile fastener coating for indoor or light outdoor environments, especially where aesthetics are important.
Used in: Finish nails, C-rings, General-purpose staples.
Hot-Dip Galvanized Finish (HDG)
This robust fastener coating submerges the fastener in molten zinc, producing a thick, durable layer that excels in outdoor or caustic settings. Although not suitable for decorative use due to its dull finish, it offers superior service life and abrasion resistance.
Used in: Framing nails, Roofing nails, U crown staples, Structural or exterior fasteners.
Mechanical Plating (also known as Mechanical Galvanizing)
This coating process cold-welds zinc to fasteners using tumbling action and chemicals, creating a uniform, matte finish. Mechanical plating is an ideal fastener coating for hardened parts, offering no hydrogen embrittlement and excellent paint or adhesive bonding compatibility.
Used in: Screws, Bolts, Nails requiring even coating and stress-free plating.
Copper-Plated Finish
This decorative finishing provides a warm, reddish-gold hue with limited corrosion resistance. While not a heavy-duty fastener coating, it blends well with corrugated cardboard and excels in light-duty or aesthetic-driven applications.
Used in: Carton closing staples and Fencing staples.
Resin-Coated Finish
A heat-activated resin coating that bonds to wood fibers upon driving, significantly increasing holding power. Available in various colors, this finishing enhances concealment and surface matching, and is widely used in fasteners for construction or furniture assembly.
Used in: Finish nails, Brad nails and Other industrial staples.
Cement-Coated Finish
This adhesive-style coating activates with heat to improve grip during driving. As a budget-friendly finisher, it offers color options like chromate, black, or silver. It's ideal for wood-to-wood and wood-to-concrete fastening.
Used in: Concrete nails, T nails, Sinker nails for framing or sheathing.
Vinyl-Coated Finish
This plasticized coating reduces drive-in friction and adds medium rust protection. It's a flexible fastener coating widely used in pneumatic nailing tools for framing and fencing applications.
Used in: Framing nails, U crown staples, Hog rings like C-rings and Omega rings.
Black Oxide Finish
Once common in decorative fasteners, this blackened finishing offers low reflectivity and mild rust protection. However, its use has declined due to environmental concerns linked to its manufacturing process.
Used in: Rosehead nails, Common nails, Screws for indoor decorative or furniture use.
Ceramic-Coated Finish (Specialty Option)
This high-performance coating is tailored for marine and chemical-heavy environments. Its multi-layer barrier provides unmatched moisture and salt resistance, ideal for long-term finishing of exterior-grade fasteners.
Used in: Screws and bolts for marine-grade or outdoor use.
Phosphate Coating (Black or Grey)
A black or grey coating that enhances adhesion for oils, paints, or adhesives. Though it offers minimal standalone protection, it is often used as a pretreatment in automotive and industrial fastener finishing.
Used in: Screws and bolts for automotive, industrial, and pre-painted applications.
Cadmium-Plated Finish
This specialized electroplated coating provides excellent corrosion resistance and high lubricity. Common in aerospace and defense fastener applications, cadmium is tightly regulated due to its toxicity.
Used in: Masonry nails, Screws, Bolts, Studs, Defense-grade aerospace fasteners.
Gold-Plated Finish
A premium finishing that offers superior conductivity, resistance to oxidation, and visual clarity. Typically reserved for electronics and precision equipment, this fastener coating serves functional and decorative purposes.
Used in: Screws for electronic, watches, and accessories, high-end mechanical assemblies.
Zinc Flake Coating
This eco-friendly, non-electrolytic coating is applied by dip-spin or spray and is ideal for avoiding hydrogen embrittlement. With outstanding corrosion resistance and recyclability, it's a modern solution in automotive and renewable sectors.
Used in: Bolts, Nuts, Screws in automotive and wind turbine applications.
Conclusion
Choosing the right fastener finishing is essential for achieving durability, corrosion resistance, and long-term performance in even the most demanding environments. Whether you're working with nails exposed to outdoor elements, staples for packaging, or screws in structural assemblies, the finishing applied directly influences efficiency, strength, and reliability. Each fastener coating—from galvanized and phosphate finishes to advanced treatments like ceramic or zinc flake—delivers specific benefits tailored to your materials and usage conditions. The right coating doesn’t just protect your fasteners—it also reduces maintenance needs, improves installation flow, and elevates the overall quality of your project.
At VIM, we specialize in delivering high-performance fasteners with engineered surface treatments that meet the evolving needs of industries worldwide. Backed by extensive expertise in Nails Finishing, Staples Finishing, Screw Finishing, and a broad range of fastener coating technologies, we offer custom-fit solutions designed for superior durability, precision, and application-specific results. Whether you're in construction, packaging, automotive, or a niche specialty field, our commitment to consistent quality and innovation ensures your fastener finishing is optimized for every environment. Ready to find the ideal fastener coating solution? Our technical team is here to support your selection and specification process—reach out to us anytime to discuss your project needs.
Article Classification
Recent Articles
- Stop Wasting Your Time! 9 Coil Nail Hacks for Faster Roofing & Crates
- Are You Confusing Pins and Brad Nails? Here's How to Tell Them Apart
- Not Sure Which Gauge to Use? These 4 Points Make It Easy
- Make Every Connection Count: 4 Clear Strategies to Choose the Best Fastener Materials
- Why Finishing Matters More Than You Think: 4 Mistakes to Avoid in Fastener Coating Selection