Choosing the Right Coil Nails: 8 Essential Factors for Your Project
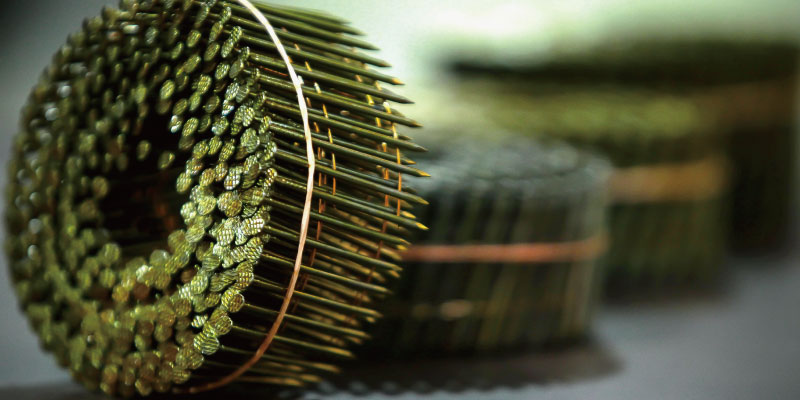
Selecting the right coil nails for your project involves understanding various key factors that impact performance, durability, and compatibility. From material types and shank styles to finish options and head types, each feature plays a critical role in meeting specific project demands. This guide explores the wide range of options available in coil nails to help you make informed decisions, ensuring your project achieves the highest standards of quality and efficiency.
Options in Coil Nails
From collation types and shank styles to coatings and finishes, each feature impacts the nail's performance and suitability for specific applications. Below, we explore the various options in coil nails to guide you in making informed decisions for your next project.
1. Material Types
- Steel: Includes bright steel for indoor use and high-carbon steel for enhanced durability and impact resistance.
- Galvanized Steel: Options include electro-galvanized for basic corrosion resistance and hot-dipped galvanized for superior outdoor protection.
- Stainless Steel: Ideal for high-humidity or coastal areas with significant exposure to moisture and salt.
- Aluminum: Lightweight and rust-resistant, suitable for projects where weight is a concern.
- Copper: Highly corrosion-resistant and used in specialized or decorative projects such as roofing.
- Vinyl-Coated Steel: Adds ease of driving and limited moisture protection.
- Wood: Provides a natural aesthetic and is typically used in applications where appearance and compatibility with wood structures are prioritized.
- Wood: Lightweight and versatile, suitable for decorative or indoor applications where aesthetics are important. Commonly used in furniture and cabinetry.
- Polymer: Lightweight and corrosion-resistant, often used in applications where flexibility and moisture resistance are required. Common in various household items and certain construction components.
2. Shank Types
- Smooth Shank: Ideal for softwoods with easy penetration.
- Ring Shank: Provides strong grip, perfect for plywood and exterior applications.
- Screw Shank: Maximum holding power, suitable for high-strength requirements.
3. Point Types
- Sharp Point: For quick driving into soft or medium-hard materials.
- Blunt Point: Reduces the risk of wood splitting, suitable for delicate tasks.
- Diamond Point: Four beveled edges, suitable for hardwood.
- Chisel Point: Flat edge reduces wood splitting, ideal for dense materials.
- Needle Point: Minimizes resistance, ideal for precision tasks.
- Clinch Point: Designed to bend and form a secure hold.
- Cut Point: Single sharp edge, minimizes splitting in hardwood.
- Flat Point: Lacks a sharp edge, suitable for controlled entry in softwoods.
4. Head Types
- Full Round Head: Provides maximum holding power and is commonly used in structural framing.
- Clipped Head: Allows for more nails per coil but may not be code-compliant in all regions.
- D-Head: Similar to clipped head but with a more rounded shape, suitable for high-density nailing applications.
- Offset Full Round Head: Offers the strength of a round head with improved spacing, ideal for tighter nail arrangements.
- Brad Head: Small, barely visible head used primarily for finish work where appearance is important.
- Cupped Head: Concave design helps grip surfaces securely, often used in roofing applications.
- Flat Head: Provides a wide surface area for greater holding power, commonly used in framing and construction.
- Bugle Head: Tapered head that prevents surface damage, typically used with drywall for a flush finish.
- Trim Head: Smaller diameter head for minimal visibility, commonly used in finish carpentry and cabinetry.
- Checker Head: Textured head for improved grip with hammers, often used in construction for better nail setting.
- Domed Head: Rounded top for aesthetic purposes, typically used in decorative applications.
- Drive Screw Head: Spiral grooves on the head allow it to screw into material, often used for extra holding strength in specific applications.
5. Finish Types
- Bright: Non-coated nails, suitable for indoor use where exposure to moisture is minimal.
- Blued: Heated to a blue-black color, providing minimal rust resistance; typically used for indoor applications or to reduce glare.
- Vinyl Coated: Aids in smoother driving and additional holding power.
- Phosphate Coated: Dark gray finish that helps improve holding power and reduces friction, commonly used for drywall and framing.
- Cement Coated: Thin layer of adhesive coating that increases holding power by creating additional grip as it heats up during driving.
- Electro-Galvanized: Thin zinc coating applied electrically, offering some corrosion resistance; suitable for light outdoor or damp environments.
- Mechanically Galvanized: Zinc particles bonded mechanically to the nail for moderate corrosion resistance, suitable for general outdoor applications.
- Copper Coated: Thin copper layer for added corrosion resistance and decorative purposes, often used for roofing and decorative applications.
- Galvanized: Provides corrosion resistance, making it suitable for outdoor and weather-exposed applications.
- Hot-Dip Galvanized: Thicker zinc coating applied through hot-dip process, providing enhanced corrosion resistance for demanding outdoor use.
- Stainless Steel: Offers superior rust resistance for highly corrosive environments.
6. Collation Types
- Wire Collated: Coil nails bound together with thin wires for strong, flexible loading and feeding in nail guns.
- Plastic Collated: Coil nails bound with plastic strips, reducing potential jamming and providing a cleaner job site.
7. Angle Types
- 0 Degree: 0-degree coil nails are aligned straight within the coil, ideal for precision work in tight spaces, such as roofing and framing.
- 15 Degrees: 15-degree coil nails have a slight angle, offering better reach and faster firing in corners and angled surfaces, making them suitable for siding and fencing.
Choosing the Right Coil Nails for Your Project
Choosing the right coil nails for your project involves considering several key factors. By understanding these options, you can choose coil nails that best meet the specific demands of your project, ensuring efficiency and durability.
Project Type
Identify whether your project involves indoor or outdoor work, heavy-duty construction, or light carpentry. This helps determine the appropriate nail material, length, and coating.
Material Compatibility
Ensure the coil nails match the type of material you are working with. For example, stainless steel or hot-dipped galvanized coil nails are better for outdoor or moisture-prone projects, while bright steel coil nails may suffice for indoor use.
Holding Power Requirements
Choose the appropriate shank type based on the needed holding power. Ring shanks and screw shanks offer higher resistance to pull-out, making them ideal for structural and load-bearing applications.
Nail Gun Compatibility
Confirm that the angle and collation type of the coil nails match the specifications of your nail gun. Most coil nails are angled at 15 degrees, but variations may exist.
Corrosion Resistance
For projects exposed to weather or moisture, opt for galvanized or stainless-steel coil nails to prevent rust and ensure long-term durability.
Aesthetic Requirements
For visible work or decorative projects, consider the finish and head type. Stainless steel coil nails may be chosen for their aesthetic appeal and rust resistance.
Why Choose VIM Coil Nails?
Vim offers a comprehensive range of coil nails tailored for various applications, ensuring you have the ideal options for both heavy-duty construction and fine carpentry. With high-quality materials like galvanized and stainless steel, diverse shank and head types, and a selection of corrosion-resistant finishes, Vim’s coil nails are designed to deliver durability, reliability, and aesthetic appeal. Whether you need strong holding power, weather resistance, or a clean finish, Vim provides the quality and versatility to make your projects a success.
Conclusion
Choosing the right coil nails requires a thoughtful balance of factors, such as project type, material compatibility, holding power, and nail gun compatibility. By aligning each element—whether it’s selecting the correct shank style for enhanced grip or a finish that ensures corrosion resistance—you can achieve the best results tailored to your project’s specific needs. For outdoor or moisture-prone projects, opting for galvanized or stainless-steel finishes enhances durability, while for aesthetic indoor projects, bright or copper-coated options may be ideal.
With Vim’s extensive range of coil nails, each option is crafted with attention to detail and performance, ensuring reliable results for both demanding and decorative applications. From collation types and angle options that support ease of use to robust materials suited for various environments, Vim coil nails deliver versatility and strength. With Vim, you’re choosing quality products that provide durability, precision, and finish essential to successful and long-lasting project outcomes.
Feel free to contact us with your requirements—we are here to assist you!
Article Classification
Recent Articles
- V Nails or Cartridge Wedge? 5 Pro Tips for Perfect Fastener Selection
- Stop Wasting Your Time! 9 Coil Nail Hacks for Faster Roofing & Crates
- Are You Confusing Pins and Brad Nails? Here's How to Tell Them Apart
- Not Sure Which Gauge to Use? These 4 Points Make It Easy
- Make Every Connection Count: 4 Clear Strategies to Choose the Best Fastener Materials